Coil Breaks
by
Esther Mar
| Sep 28, 2017
What are Coil Breaks and why are they objectionable?
- Coil Breaks are creases which appear as lines transverse to the rolling direction and generally extend across the width of the steel.
- If a coil is sheeted and used in flat form the condition is considered unsightly.
- Coil Breaks are purely cosmetic.They are non-injurious and will not affect formability.Coil Breaks will not affect the integrity of formed parts.The presence of Coil Breaks is a clear indication of very formable and ductile material.
What causes Coil Breaks?
- Skin rolling or temper rolling can be used to alleviate coil breaks in two ways.A small cold reduction is applied to create numerous nucleating points for Coil Breaks that are so small so as not to be obvious.In addition, pre-existing Coil Breaks are flattened and masked.
- In order to guarantee freedom from Coil Breaks on hot rolled steel the product must be skin rolled or temper rolled.
- Coil Breaks are not usually seen on fully processed cold rolled sheet because the processing includes temper rolling after annealing.Similarly coated products are either tension leveled or temper rolled in line.
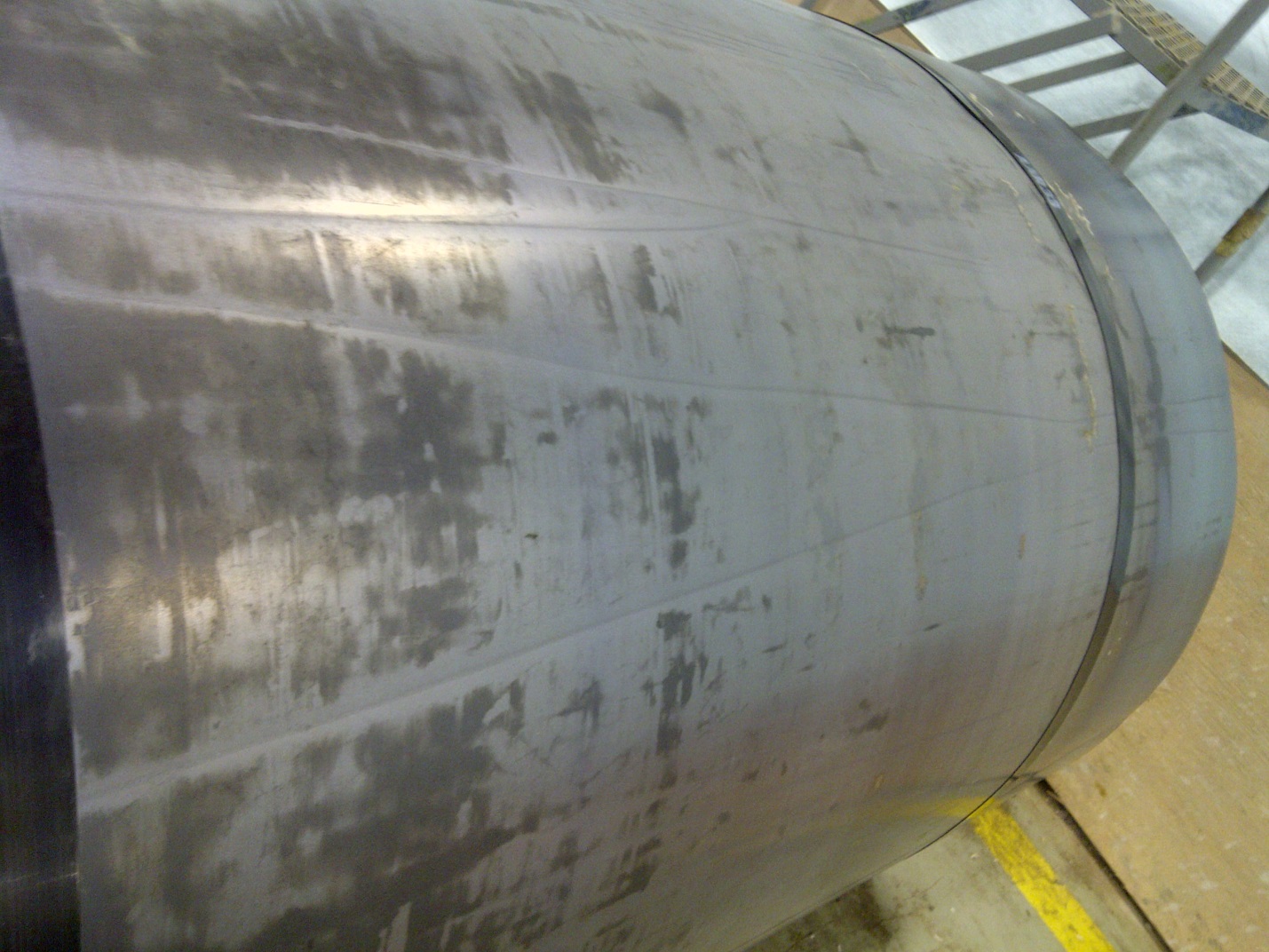