by
Esther Mar
| Jul 05, 2018
Galvanized sheet sometimes exhibits a surface imperfection that appears as short black marks, usually in patches. This condition has several names in addition to transit abrasion including fretting corrosion, friction oxidation, wear oxidation and chafing. These terms refer to the root cause of the problem, which is related to friction between contact points, similar to galling. The condition is characterized by a mirror image on the reverse side of the sheet. The reason the term corrosion or oxidation is used is that this imperfection is associated with the buildup of oxide particles.
Fretting corrosion is the most technical name. It refers to corrosion damage at the high points of contact surfaces. It occurs under load, under conditions of repeated relative motion of the surfaces in contact with each other, and these two conditions must be sufficient to produce deformation of the surface, which is likely with galvanized sheet because the zinc coating is fairly soft. This mechanism can affect any two surfaces that are not intended to move against each other and, in the case of machinery, can prematurely wear out parts.
Fretting corrosion has been observed on galvanized steel in both coil form and bundles of cut lengths. This condition is never seen on the galvanizing line, almost always being found in a customer’s plant. The repeated motion comes from vibrations that occur during shipment of the product. The condition is rare in the case of truck shipments, generally being prevalent when product is transported by train and ship where it incurs vibrations for long periods of time. The load comes from the weight of the coil (or stack of sheets). This is why transit abrasion is observed mostly on the outer portion of the coil at the bottom half of it (or bottom portion of the bundle).
There are measures that can prevent or minimize transit abrasion, all targeting reducing load or minimizing friction. Actions that are very effective are designing support saddles to reduce concentrated point loading on the bottom of coils and avoiding stacking during transit. Other measures are reducing the coil size and oiling the material, although these methods are not always practical or possible.
There are two mechanisms that operate to produce fretting corrosion: wear-oxidation and oxidation-wear. The first proposes that cold welding occurs at the contact points with small fragments of metal being removed and that these immediately oxidize. The second proposes that the normal oxide layer already present on the galvanized sheet is ruptured at the high points under load and vibration, thus producing oxide particles.
Fretting corrosion is a cosmetic condition. There is no evidence that it is detrimental to the corrosion resistance of the galvanized sheet.

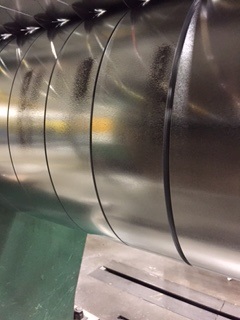