by
Esther Mar
| Oct 24, 2017
Many breakage problems are created by tension along a sheared edge or flange. Some of these problems are caused by a burr due to stamping dies that are dull or have incorrectly set clearances. When the burr, which has low ductility, is subjected to high strain, as can occur during forming, a crack may develop. If the crack occurs in an area that is not subsequently trimmed off the result is scrap or rework. Removing the burr will reduce the length of the crack but may not eliminate it. This is because even though the area where the greatest amount of cold work, the burr, has been removed, severe deformation of the grain structure may extend well into the base metal and reduce the ductility of that area as well. To eliminate tearing of the blank during forming, the burr and cold worked area must be completely removed or, preferably, be prevented from developing. This can be done by keeping the dies sharp and adjusted.
Sometimes even good edges are susceptible to splitting. In this case it is worth reviewing the part and blank design. Part designers often have latitude in specifying the final shapes of stampings but even where that is not possible blank shape optimization may be possible by conducting a forming severity analysis. Based on the part geometry and material properties a finite element model can be developed for the forming stage and analyzed to assess the effect of blank shape redevelopment in minimizing edge strain at the location of the splits.
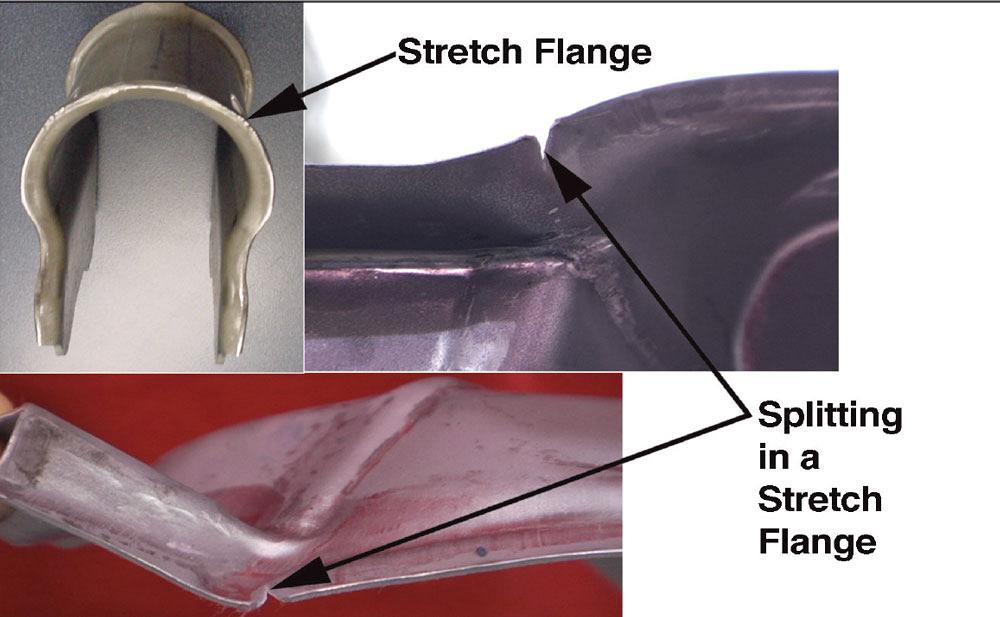
Examples of splitting at a stretched edge or flange

Schematic cross section of a sheared or blanked edge
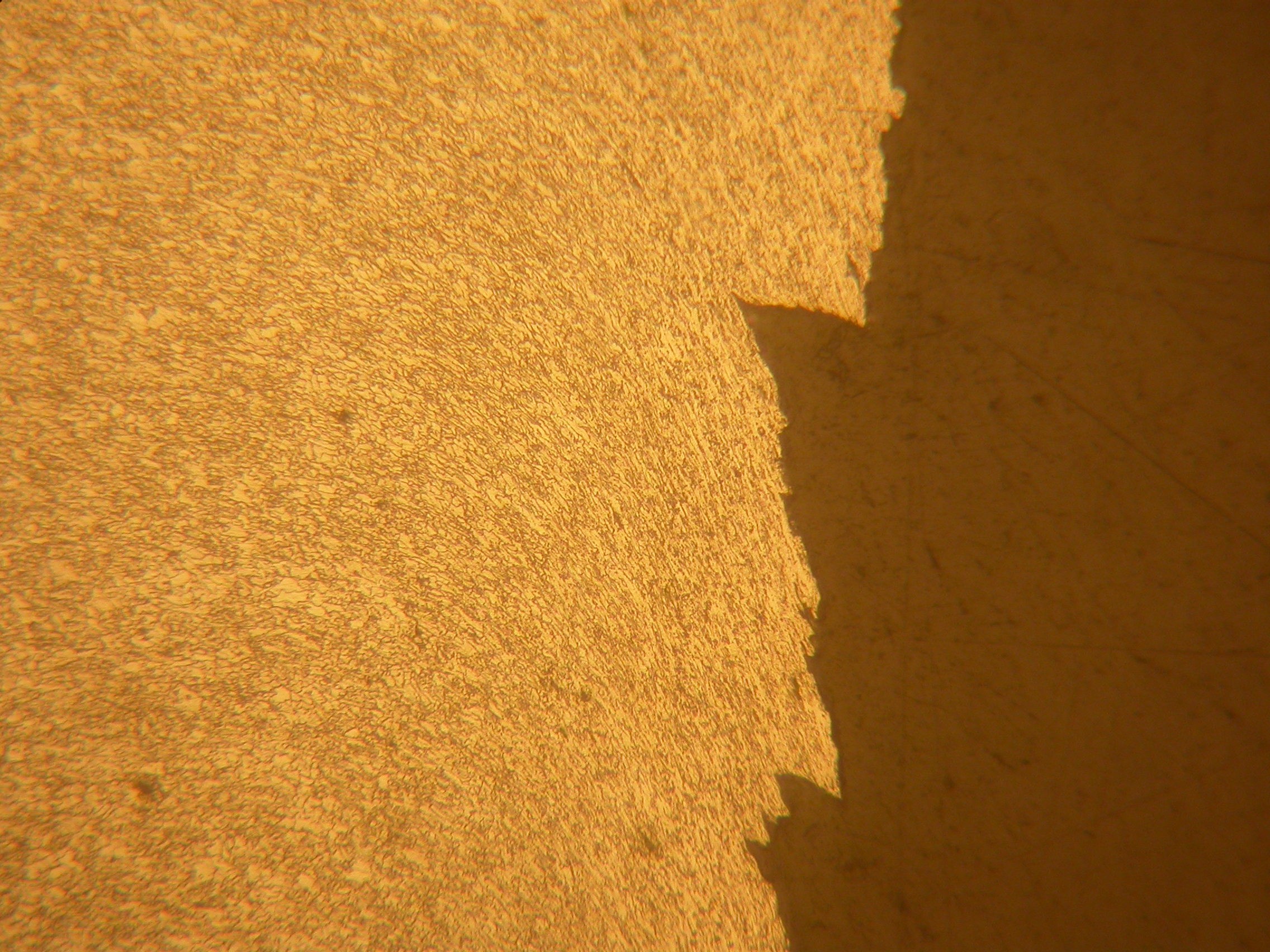
Photomicrograph showing a cold worked microstructure in the fracture portion of the blanked edge